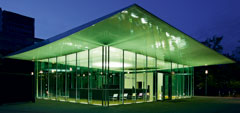
Jörg Pfäffinger
Die Novartis AG verwandelt ihr Werkareal St. Johann am Hauptsitz in Basel in einen Campus des Wissens, der Innovation und der Begegnung. Die Forschung und Entwicklung, das Marketing und die Verwaltung sollen an diesem Standort ausgebaut und in einem attraktiven Umfeld etabliert werden. Der Philosophie des Unternehmens nach Offenheit und Transparenz folgend hat man in den Führungsetagen ein Faible für Glas. Bereits an der Fassade des ersten Gebäudes aus dem Jahr 2005 lassen farbige Glasscheiben in unterschiedlichen Formaten den Bürobau schillernd, aber dennoch dezent erscheinen.
Anfang dieses Jahres wurde ein weiteres Projekt im Rahmen der Umwandlung des ehemaligen Industriestandortes übergeben: das Empfangsgebäude des Novartis Campus. Der Architekt Marco Serra übertrug hier dem Baustoff Glas neben der optischen Aufgabe, Transparenz und Leichtigkeit zu offerieren, auch eine tragende Rolle. Marco Serra: „Es ging mir nicht darum, einfach ein Glashaus zu erstellen. Der erste Gedanke war, die Chance zu nutzen, die ein kleines Gebäude bietet. Nämlich die, dass man im Vergleich zu großen Gebäuden keine tragende Grundstruktur aus Stahl oder Stahlbeton benötigt.“ Deshalb konnte die Stabilisierung gegen Wind und Erdbeben vollständig über die gläsernen Außenwände erfolgen. Christoph Haas vom Ingenieurbüro Ernst Basler + Partner ergänzt: „Oft genug sind Glasbauten an Massivbauten angebunden, über die die Windkräfte abgeleitet werden. Das Novartis-Gebäude hingegen steht frei, und die Kräfte werden horizontal und vertikal über die Glasfassade abgeleitet. Derartige Bauten gibt es weltweit nur sehr wenige.“ Und die erste „stürmische“ Bewährungsprobe hat die Glaskonstruktion beim Orkan Kyrill schadlos bestanden.
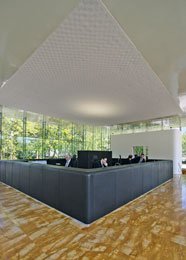
Meilenstein des Glasbaus
Die Steifigkeit der Glasfassade wird durch Glasschwerter erreicht, die zusammen mit dem Fassadenglas U-Träger bilden. Daher ist die Fassade aus U-förmigen Elementen zusammengesetzt: dem Fassadenglas (mit dem Aufbau acht Millimeter ESG außen und VSG mit 2 x 12 Millimeter TVG innen) in Kombination mit je zwei aussteifenden Glasschwertern. Das VSG ist am Fuß der Fassade in ein Stahlteil eingebunden, das im Boden des Gebäudes verankert ist. Das Achsmaß der Fassadenelemente beträgt 1,70 Meter; die Elemente sind 4,90 Meter hoch. Um sie später einfacher auswechseln zu können und auch die Herstellungskosten nicht explodieren zu lassen, gibt es nur drei Elementtypen. Der Unterschied besteht lediglich darin, dass die Oberkante der Glasbauteile von außen betrachtet horizontal oder in die eine oder andere Richtung geneigt ist. Erreicht hat man das, indem die Gläser nicht in der Krümmung geschnitten wurden.
Eine weitere Besonderheit ist die Ausbildung der Gebäudeecken. Im Vergleich zu den Glasschwertern an den gradlinigen Glaswänden wurden die Glasschwerter in den Eckbereichen breiter und außerdem aus Isolierglas gefertigt. Einer umfangreichen Qualitätssicherung wurde außerdem die Fugendichtung aus Silikon unterzogen. Neben der abdichtenden Funktion hat das Material auch eine tragende Aufgabe und selbst der gewählte hellbraune Farbton musste mit der Innenausstattung harmonieren. Bernd Feigel, Geschäftsführender Gesellschafter der Firma Glas Marte, die die Fassade herstellte: „Für uns war dieses Projekt ein Meilenstein im konstruktiven Glasbau. Nie zuvor habe ich erlebt, dass er in Elementbauweise betrieben wurde.“
Flexible Verbindung
Viel Detailarbeit verlangte besonders die Schnittstelle zwischen Glasfassade und Dach. Der nach unten gewölbten Dachform muss die Glasfassade entsprechend folgen. Das erforderte spezielle Konstruktionen, um die Horizontal- und Sogkräfte aufgrund der unterschiedlichen Temperaturdehnung der Materialien, des Glases und des glasfaserverstärkten (GFK) Kunststoffs des Daches, ausgleichen zu können.
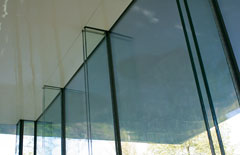
Dazu wurde im Dach ein Doppelsteg vorgesehen, der die Vertikalkräfte über ein Gleitlager, ein Stahlband und ein Gießharz (für den Toleranzausgleich) ableitet. Die Anbindung von Dach und Fassade ist so gestaltet, dass sich das Dach sowohl parallel zur Fassade verschieben als auch die Fassade die Windlast an das Dach abgeben kann. Das Stahlband hat die Aufgabe, die Kraftübertragung auf mehrere Gläser zu verteilen. In jeder der vier Glasfassaden existiert in der Mitte ein Punkt, an dem die Fassade über das Stahlband starr mit dem Dach verbunden ist. Hier werden die Windkräfte an das Dach übertragen. Doppelsteg und Stahlband wurden bereits werkseitig in das Dach eingelegt.
Das Dach sollte im Werk mit hoher Maßgenauigkeit vorgefertigt sein und bei ausreichender Tragfähigkeit und Steifigkeit ein geringes Gewicht aufweisen. Dazu Richard Steger, dessen Unternehmen Scobalit das Dach fertigte: „Es besteht aus einzeln zugeschnittenen Polyurethanschaumblöcken mit unterschiedlichen Gewichten und Fräsungen. Die Anforderungen an die Statik konnten wir durch spezielle Laminattechniken sowie die Verwendung unterschiedlicher PU-Schaumdichten erreichen.“
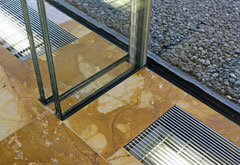
Fixe Verbindung
Zugstangen aus Stahl zwischen den Glasschwertern verhindern, dass sich das Dach unter Temperatureinfluss stark verkrümmen und gegebenenfalls von der Fassade abheben könnte. Zusätzlich sichern sie das Dach gegen Windsog. Architekt Serra: „Es ist interessant, dass das Glas der Fassade offensichtlich nicht die Problematik des Drucks, sondern die des Zugs hat. Das Dach muss eher gegen die Sogwirkung des Windes geschützt werden.“ Das wird mit sehr kleinen technischen Elementen bewerkstelligt: Die zwischen den Glasschwertern befindlichen Zugstangen sind mit Kunststoff umhüllt, wodurch die Statik invertiert und das Dach fixiert wird. Unten sind die Zugstangen mit Federn befestigt. Denn wenn sich die Stahlstange bei Kälte verkürzt, würde sie ohne Feder einen zu hohen Druck auf die Fassade ausüben. Im Dach sind die Zugstangen in von Hand einlaminierten Stahleinlagen befestigt.
Spezielle Türen
Die großen Türen aus Isolierglas sind eine weitere Spezialität der Fassade: Auf der Südseite befindet sich eine zweiflügelige Ausführung mit einer Achsmaßbreite von 2 x 1,70 Metern und drei Metern Höhe, eingefasst von einem Stahlrahmen, chromstahlverkleidet und motorisch angetrieben. Sie ist ein Notausgang mit zusätzlichen Anforderungen an die Sicherheit. Christoph Haas vom Ingenieurbüro: „Die Konstruktion war eine fassadenplanerische Herausforderung, denn über der Tür befindet sich bis zum Dach hinauf eine Glasfläche, die ebenfalls Lasten abträgt.“ Auf der Nordseite des Gebäudes ist als Windfang eine drei Meter hohe Rundschiebetür eingebaut. Sie wird ebenfalls von einem festen Türrahmen umschlossen. Auch diese 1,50 Meter hohe Fassadenfläche zwischen Tür und Dach leitet Kräfte ab. Der Öffnungsmechanismus der Flügeltür auf der Südfassade wird durch einen Türsensor im Dach ausgelöst, dessen Kabelführung zwischen den Glasschwertern herunter in den Türrahmen erfolgt.
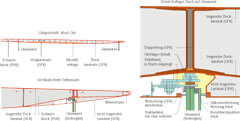
Dach aus GFK-Composite
Den gestalterischen Anspruch, den der Architekt an das Dach stellte, sollte die Qualität einer vor Ort gebauten Konstruktion vermitteln. Über diese Idee kam man zuerst auf die Materialien und erst dann auf die Technik. Glasfaserverstärkte (GFK) Composite-Materialien erlauben es, das Dach monolithisch und fugenfrei auszuführen und so die Leichtigkeit des Glases hervorzuheben. Das weiße, 400 Quadratmeter große GFK-Dach erinnert an eine angeschnittene Flügelspitze, denn drei von vier Dachkanten laufen rund aus. Das 28 Tonnen schwere Dach wurde in vier Teilen fast komplett im Werk vorgefertigt. Grundlage der Konstruktion sind 460 Polyurethan-(PUR-)Blöcke, von denen mindestens 400 eine individuelle Form aufweisen. Obwohl die Grundform des Daches fast symmetrisch ist, sitzt die Fassade darunter nicht symmetrisch. Deshalb gibt es kaum Blöcke, die gleich sind.
Die statischen Anforderungen an die Konstruktion wurden durch die Verwendung spezieller Laminattechniken unterschiedlicher PUR-Schaumdichten erreicht. Die PUR-Schaumblöcke wurden einzeln mit bis zu zwölf Lagen Glasfasergewebe hochwertigster Qualität umwickelt und in Handarbeit laminiert. Dadurch entstanden an den Verbindungsflächen der Blöcke Stege, die zusammen mit den Deckschichten die Tragstruktur bilden. Diese Struktur erlaubt die besondere Gestaltung, dass das Dach trotz geringer Konstruktionshöhe an der Südseite um fünf Meter die Fassade überragt.
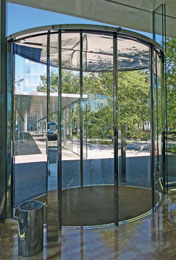
Wege der Kommunikation
Die technische Kommunikation mit den beteiligten Herstellern erfolgte auf klassischem Weg über Pläne und Excel-Tabellen und nicht über geometrische Daten. Die Sollhöhe an jedem Auflagerpunkt wurde im Tabellenformat angegeben. Die Geometrie des Daches und der Auflagerpunkte ist keine definierte geometrische Form, aber sie ist berechenbar. Die Daten für die Kommunikation, die das Ingenieurbüro lieferte, entsprachen keinem 3-D-Modell, bei dem man die aktuelle Höhe erst herausmessen muss. Das wäre nicht rationell gewesen. Die Geometrie war in Parametern aufgebaut, sodass man die Einzelpunkte leicht ausrechnen konnte. Diese Vorgaben erwiesen sich für den Hersteller des Daches bei der Positionierung der Auflagerpunkte besonders hilfreich.
Durch die präzise Vorarbeit der Planer, die die zahlreichen Einzelkomponenten äußerst fundiert und gut durchdacht bereits bei der Planung berücksichtigt hatten, konnte ein außerordentlich hoher Vorfertigungsgrad von Dach und Glasfassade erreicht werden.
Projektpartner
Bauherr: Novartis Pharma Schweiz AG, Basel
Architekt: Marco Serra, Basel
Planung: Ernst Basler + Partner AG, Zürich
Ausführung Dach: Scobalit AG, Winterthur
Ausführung Fassade: Glas Marte GmbH, Bregenz
Technische und wissenschaftliche Begleitung Dach: ETH Lausanne, Labor für Composite-Tragwerke CCLab,
Prof. Dr. Thomas Keller
Die kooperative Leistung der Projektpartner erfuhr im April ihre Anerkennung: Das futuristische Dach des Novartis Empfangs-
gebäudes schaffte es im internationalen Umfeld des JEC-Award 2007 in Paris unter die drei Finalisten
Buchtipps
Jan Wum
Glas als Tragwerk
Das Buch gibt erstmals eine Anleitung zum Planen und Gestalten von Glastragwerken. Die Konstruktionen zeigen neue ästhetische Qualitäten, die ein neues Kapitel der Glasarchitektur einläuten.
2007, 69,90 €, Birkhäuser
Glasklar
Das Buch verschafft einen Überblick über den Standder Glastechnik und das Spektrum an Produkten sowiederen Anwendungsmöglichkeiten in der Architektur.
2003, 39,95 €, DVA